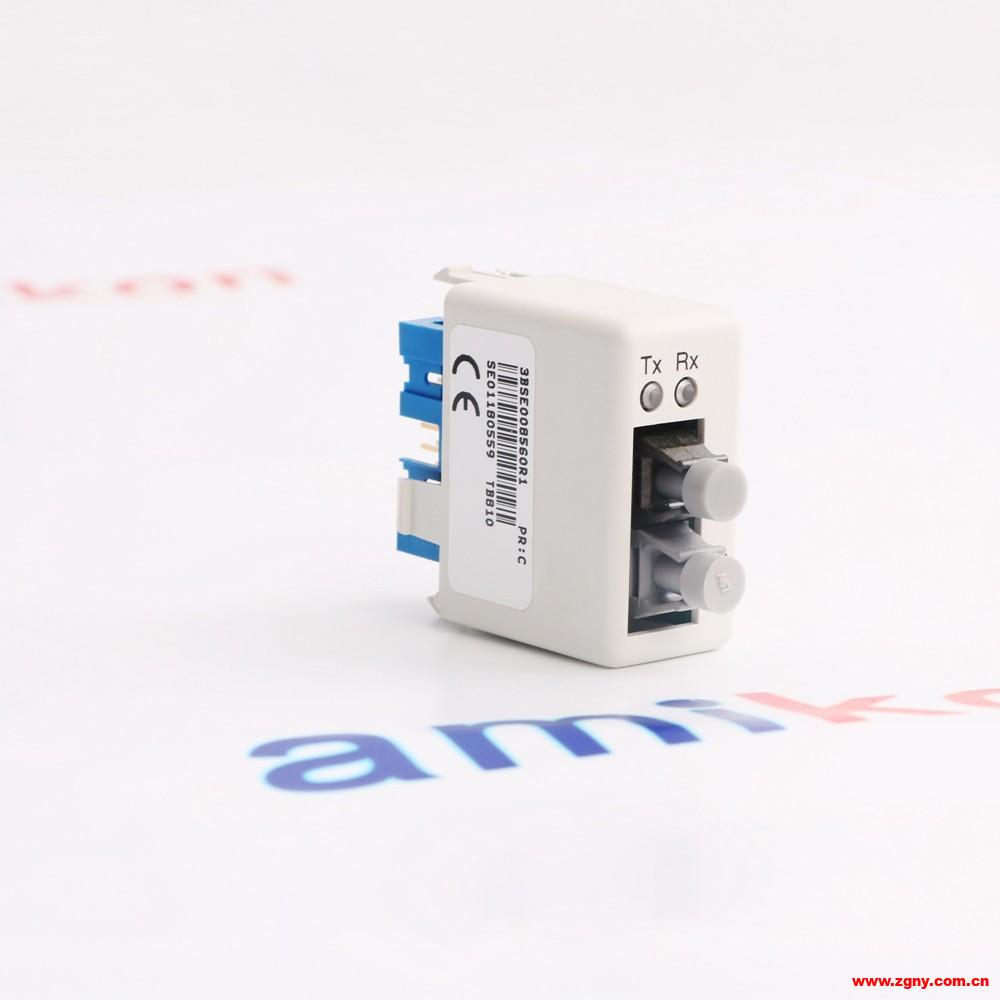
VM600 CMC16 200-530-100-014
==========★Company Profile
For details, please deduct her Xu Xiaoyan
Contact her (same number on WeChat)
Are you looking for cost savings and more effective optimization of the business process of purchasing spare parts?
We can optimize your procurement process through e-commerce promotion,
Thus your direct and indirect costs. Provide a series of links to the spare parts you need. In addition, we have established links with more overseas suppliers.
Our e-commerce consultant will be happy to discuss your needs for spare parts with you.
+ Usability, + Responsiveness: Our main task is your satisfaction!
Our supply chain platform can ensure that you optimize the delivery of industrial parts cycle.
It plays a very important role in the automatic control system. Therefore, the correct choice of PLC is very important.
Faced with the most advanced types of PLCs from many manufacturers, they have their own advantages and disadvantages, which can satisfy the most advanced needs of users, but they are incompatible in terms of form, composition, function, network, and programming. , Without a consistent specification, horizontal comparison is impossible. Here are some opinions on PLC selection in the planning of automatic control system, which can be used as a reference when selecting PLC.
Able to compare the following aspects to choose a suitable product.
1. The amount of work
This is particularly important. At the beginning of the automatic control system planning, there should be an accurate statistics on the number of control points (digital and analog). This is often the primary condition for selecting a PLC. Generally, a PLC with 10% to 30% more control points should be selected. There are several considerations:
1. Able to compensate for missing points in the planning process;
2. It can be ensured that there can be a replacement point when there is a failure at a certain point in the running process;
3. The need to increase points in the future.
2. Operating environment
The operating environment is the hard target of PLC operations. The automatic control system frees people from busy work and harsh environments. It requires the automatic control system to be able to get used to the messy environment, such as temperature, humidity, noise, signal shielding, operating voltage, etc. The various PLCs are not the same. Be sure to choose products that are accustomed to the practical operating environment.
3. Communication network
Nowadays, PLC is no longer simple on-site control. PLC remote communication has become a problem that the control system must solve. However, the communication protocols drawn up by various manufacturers are very different and have poor compatibility. At this point, the following aspects should be considered first:
1. Communication between products of the same manufacturer. Each manufacturer has its own communication protocol, and there is more than one. This performance is obvious on large and medium-sized computers, but not the same on small and micro computers. Some manufacturers often do not have a relatively simple communication that is different from other protocols because of capacity, price, function and other considerations. Therefore, the primary consideration in this regard is the communication between different types of PLCs from the same manufacturer;
2. Communication between products of different manufacturers. If the planned automatic control system is part of the transformation of the existing automatic control system, and the PLC selected is different from the original system, perhaps two or more PLCs are required in the planning, and a different manufacturer’s PLC is selected. Products, which need to consider the communication issues between products of different manufacturers;
3. Whether it is beneficial to the future. Because the communication protocols drawn up by various manufacturers are different, and there is no consistent international standard, so the PLC selection is greatly restricted. It is necessary to consider a communication protocol that has a large impact, has development, is fully functional, and is close to common use.
FA3S VAM-0070
FA3S VAM-0080
ABB DSQC 368 DSQC368 3HAC2183-1
ABB DSQC 373 DSQC373 3HAC3180-1
B&R AF101 7AF101.7
COVAL GVMAXSP345V2 A00907769
MICATRONE MICOFLEX MF-PD MFPD 60-5426-99
HAWA PGMJ-R PGMJR 1018-0002-00-00
BECKHOFF CP9035 9037B
COGNEX DM8100 825-0136-1RH
KEB F5 INTERBUS 00.F5.060-4001
SICK CDF600-0300
E1009950202
SIEMENS 6SE6420-2AD22-2BA1
SIEMENS 6ES7 214-1BD22-0XB0
FUJI ELECTRIC FRN2.2G11S-2
IPF PE280141
YOKOGAWA PW302
ABB 1SAJ510000R0400 UMC22-FBP.0 D4 UMC22FBP0D4
AMK KW-R03 KWR03 46458-0822-1124251
SIEMENS CPU 413-1 6ES7 413-1XG02-0AB0
REXROTH VT 5002 VT5002 VT-5002-25/R5E
NUM AXES CNA14BTS FC200822 E 200822D26
SIEMENS 6FX2001-5QP12
NUM ENTREES V3 201182 200428C26 FS-200428/E
HOMAG AP04-0018 CAN-20-A-S03V01.02-IP53
NUM ENTEREES V2 200429 FS-200428/D
MITSUBISHI Q172DCPU
MITSUBISHI Q13UDHCPU
SIEMENS 6DR5020-0NG00-0AA0
B&R MCPU30-0
SIEMENS 6AV6 642-0BC01-1AX1
SIEMENS OP 393-III 6ES5 393-0UA14
SEW MDX60A0075-5A3-4-00
LEUZE IPRK 92/4 S.1 50020358 IPRK924S1
SIEMENS 6FX2001-5FP12
OMRON F10-S30R
B&R MCPEA6-1
SIKO AP04-0002
LENZE 33.8204_E
COGNEX DM302X 825-0300-1R L 821-0087-3R E
HITACHI HIZAC CMP-E2 -E3 33020650-1
Bone screws, also known as fracture fixation screws, are commonly used in clinical practice to fix orthopedic implants.
Bone screws are usually used to fix internal fractures or dislocations by directly screing into two different bone blocks or fixing an internal implant such as a bone plate to achieve fracture fixation, position the bone and promote its healing. Bone screws are used in a wide range of areas, including the shoulder, elbow, hip, knee, spine, etc. For example, pedicle screw systems are used for spinal fusion, and compression bone screws are commonly used for foot and ankle surgery or fixation of other fractures under pressure. Similar to traditional mechanical screws, the main structures of bone screws also include nail cap, nail body, and nail tip. Screws can be used to fix bone plates or bone fragments. When used for the former, they are called plate screws, and when used for the latter (to prevent the collapse of bone fragments), they are called positional screws. The latter can be inserted into the plate holes, and can be placed on the bone alone (also known as compression screws). Compression screws can be used to increase interfragment pressure.
(1) The screw cap
The screw cap has three main functions: the first is to optimize the force. The protruding cap makes the contact area between the screw and bone larger, increases the load area, optimizes the local force at the screw insertion site, and reduces the risk of bone rupture caused by excessive stress. The second is the positioning effect. The prominent cap makes the bone nail can only be screwed into a certain depth to prevent the whole bone nail from being screwed into the bone completely. The third function is to provide the position of force application by rotating the force groove at the cap to move the bone nail forward and drive it into the bone. Now, the force groove is mostly inner hexagonal, which does not require axial force to maintain the actuator in the center position and is suitable for a wider range of fractures.
(2) Screw the body
The size of the nail body determines the strength and fatigue resistance of the bone nail. The larger the diameter of the nail body, the stronger the strength will be, and the corresponding fatigue resistance will be better. In addition to the diameter of the nail body, the pitch and tooth depth of the screw body thread are also the key parameters of the nail body design. Different thread design has an important effect on the pressure and occlusal performance of the screw.
(3) Screw tip
Tapping is the process of phalangeal nail cutting thread in the bone. According to the shape of the nail tip, the bone nail can be divided into self-tapping nail and non-self-tapping nail. The nail tip of the self-tapping nail is sharper and can be directly screwed into the bone without pre-drilling. Usually, self-tapping screws are used for Cancellous bone, and the bone is compressed when the screw is inserted, so as to increase the bone density of the occlusal part locally and enhance the occlusal effect. However, when inserting screws in Cortical bone, the screw channel is generally pre-punched, and then the bone screw is screwed. Usually, the self-tapping screw is not directly used to prevent the bone screw from being stuck or damaged because the cortical bone is too hard.
Bone Screw,Cancellous Screw,screws in bone,Cortical Screw
Jiangsu Aomed Ortho Medical Technology Co.,Ltd , https://www.medthofixation.com