Guide:
Recently, the Chinese Antibody Association published an article describing that the continuous manufacturing process has been promoted by the FDA: the continuous manufacturing process has become an extremely successful production model in many other industries based on its stable and high efficiency. However, for a long time, the pharmaceutical industry has been criticized by the industry for its strict supervision and regulatory requirements, so most of them are still based on batch production. In recent years, with the industry's increasing emphasis on capacity efficiency and production costs, the biopharmaceutical industry is increasingly paying attention to continuous processes, hoping to improve production efficiency and equipment utilization, and there have been cases showing specific continuous technology integration. After the existing biopharmaceutical production process, many advantages have emerged. As a global leader in drug regulation, the FDA has been a strong advocate of continuous manufacturing processes. As early as 2017, the FDA issued a draft for continuous manufacturing (CM); in 2018, the FDA provided nearly six million dollars to three consecutive manufacturing projects to help implement innovative technologies to improve product quality. And modernize the industry; On February 26, 2019, the FDA issued a draft key guideline for CM, Quality Considerations for Continuous Manufacturing, which will surely play a huge role in driving this technology, while FDA Director Scott Gottlieb and Director of the Center for Medicine Janet Woodcock is also a high-profile platform for CM. In the statement issued with the guide, the advantages of continuous manufacturing are repeatedly emphasized. It seems that CM may not be far behind. Fortunately, thanks to nanotechnology's breakthroughs in nanomaterials and bonding, UniMab Protein A affinity chromatography media is particularly suitable for continuous column chromatography due to its many unique advantages. system.
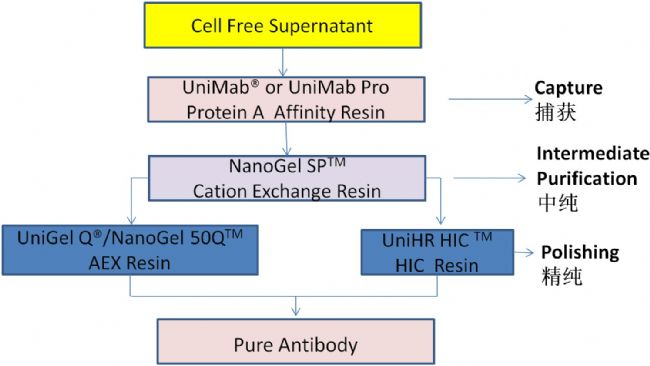
Reduce costs and improve efficiency: the necessity and urgency of implementing continuous manufacturing processes
Reducing costs and improving efficiency have always been important appeals for pharmaceutical companies. Although their products are particularly industry-specific due to their personal health and safety, they have to be too conservative due to strict regulatory and regulatory requirements of the drug regulatory authorities. But as everyone knows, people in the industry have been searching for "cost reduction, efficiency improvement" and so on. Taking biological products as an example, after years of efforts, researchers have optimized the production efficiency and cost of their upstream research and development stage to an extremely ideal level. The ceiling effect is prominent, but there are few achievements in the downstream separation and purification, production cost and efficiency. There is still a lot of room for optimization. In addition, studies have reported that the cost of separation and purification of biological products downstream exceeds 80% of the total production cost. Therefore, institutions and enterprises including the FDA have begun to turn to the research and promotion of continuous manufacturing processes. Based on this positive thinking, the continuous application of continuous chromatography in the field of downstream separation and purification will be increasingly accepted by the majority of biopharmaceutical companies and research institutions, and become one of the mainstream trends in the current and future development.
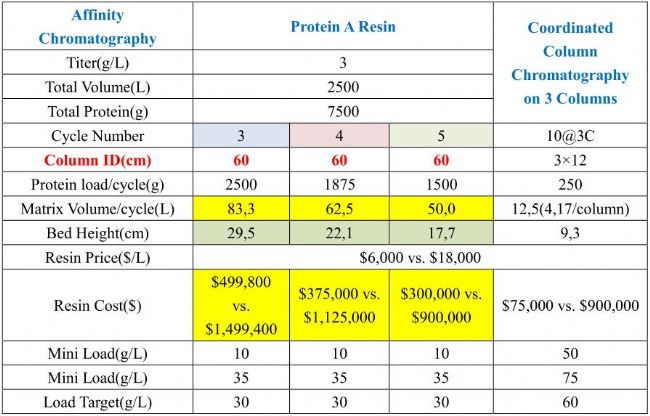
Introduction to continuous chromatography
It is well known that traditional chromatographic separation techniques are carried out using a fixed chromatographic column, which first enters a certain amount of material and then elutes continuously with an eluent. At the same outlet, different product components can be received at different time intervals. This process is obviously time consuming. The continuous chromatographic separation technique uses different substances to have different partition coefficients in the system composed of the stationary phase and the mobile phase. When the two phases move relative to each other, the materials move with the mobile phase and are carried out between the two phases. The distribution is repeated several times, so that the substances are separated. In actual production, continuous flow chromatography can achieve higher yields and lower costs, which is achieved by reducing the amount of Protein A filler and buffer consumption. Because of the stable operation, it can better guarantee the quality of the product. Consistency and significantly increase the yield of downstream purification. Traditional chromatographic separation methods usually load and elute a single column sequence, which significantly limits the degree of media utilization. Continuous chromatographic techniques use multiple columns in parallel for parallel loading and elution. The way to undoubtedly maximizes the utilization of the media.
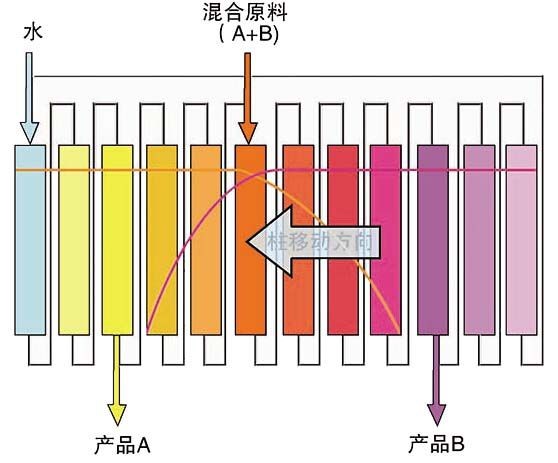
Schematic diagram of continuous chromatography
Although traditional chromatographic separation technology is widely used, it still has a series of problems to be solved:
The solvent consumption is large, and the comprehensive production cost remains high;
The filler is used in a large amount, the output per unit filler is small, and the industrial production cost is further increased;
Some low-resolution varieties are limited in separation and cannot be industrialized;
For some special samples (such as chiral drugs), there is no good solution and so on.
However, continuous chromatographic separation technology can achieve continuous use of materials. The application of the same scale of fillers and solvents can greatly improve the sample throughput. For some chemically similar components, the ideal resolution and sample recovery rate can still be obtained. The technology can mainly solve the problem of continuous separation of large and small molecular raw materials and functional sugars, and reduce the utilization of buffers, improve the utilization rate of fillers, and reduce production costs efficiently. Currently, it has been widely used in petrochemical industry. Food engineering and biochemical industries, such as:
Separation of sugar alcohols: fructose syrup, inulin, oligofructose, trehalose, arabinose, xylitol, ribose, etc.;
Separation of chiral drugs and natural products: paclitaxel, fish oil, paeoniflorin, soy lecithin, fluoxetine, ketoprofen, etc.;
Fine chemicals: flavors, pigments, unsaturated fatty acids, etc.;
Petrochemical: PX and its analogues, carbon five carbon six intermediate isomerized alkanes, etc.;
Biological macromolecules: protein polypeptides (affinity chromatography), nucleic acids, and the like.
Ideal continuous chromatographic media: UniMab Protein A affinity chromatography media
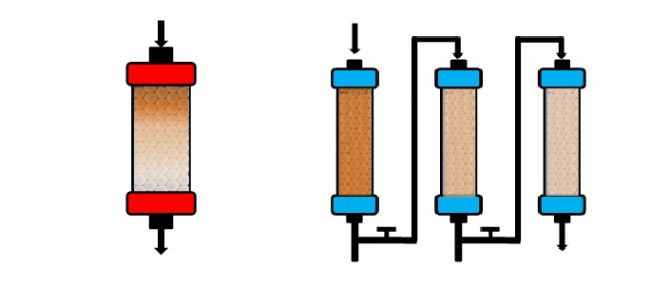
Traditional batch chromatography (left) new continuous chromatography (right) elution concept map
In the traditional batch chromatography method, the experimenter can only use a single column for separation and purification, and can only be eluted in sequence when loading. Although this method is suitable for most separation and purification, it is suitable for purification medium. The utilization rate is not high; in the new continuous chromatography method, the experimenter can simultaneously use multiple columns in parallel and perform sample loading and elution, and the entire elution process is continuously performed continuously. This ensures that the use of less buffer is used to maximize the utilization of the packing. This new chromatographic scheme has proven to be very effective in the separation of chiral and saccharide compounds, especially in the case of monoclonal antibody capture. Monodisperse UniMab affinity media have a unique set of advantages such as uniform particle size, high column efficiency, good column and column repeatability, high mechanical strength, low back pressure, and high flow rate downloads, just to meet the high flow rate of continuous chromatography. Claim.
Continuous chromatography with monodisperse UniMab dramatically increases productivity and media utilization
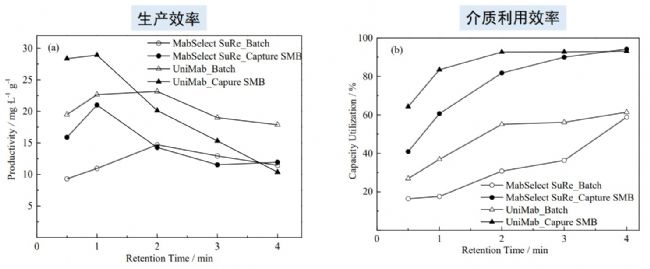
Comparison of production efficiency and media utilization efficiency between monodisperse UniMab chromatography media and polydisperse soft matrix media
Because the new continuous chromatography has many obvious advantages over traditional chromatography, it can bring higher production efficiency and media utilization. The above characteristics have also been confirmed in the practical application process. As shown above, continuous chromatography has higher productivity and media utilization efficiency than traditional chromatography, while monodisperse UniMab chromatography media exhibits higher retention time over most retention times than polydisperse soft media. Production efficiency and media utilization, and it is clear that monolithic media have significant advantages over polydisperse media, whether by new continuous chromatography or conventional chromatography.
Continuous chromatography with monodisperse UniMab significantly reduces mobile phase consumption, high efficiency and environmental protection
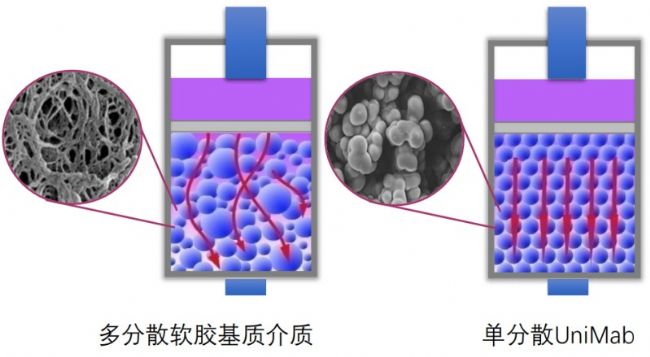
Schematic diagram of media chromatography elution in monodisperse and polydisperse systems
Thanks to the monodisperse medium manufactured by Nano Micro, the UniMab affinity chromatography medium exhibits a better orderly elution behavior during the elution of the soft matrix matrix affinity media, vortex diffusion, longitudinal Both diffusion and mass transfer resistance are significantly reduced, so monodisperse systems are more likely to achieve high chromatographic performance, low back pressure and other ideal chromatographic properties during the elution process. As shown in the figure below, continuous chromatography saves buffer consumption more than traditional chromatography, and monodisperse UniMab affinity media can significantly reduce buffer consumption compared with polydisperse soft affinity media, which not only saves manpower and material input costs, It also saves more environmental costs such as late waste liquid treatment. It can be said that monodisperse chromatography packing is an ideal choice for separation and purification in the modern pharmaceutical industry.
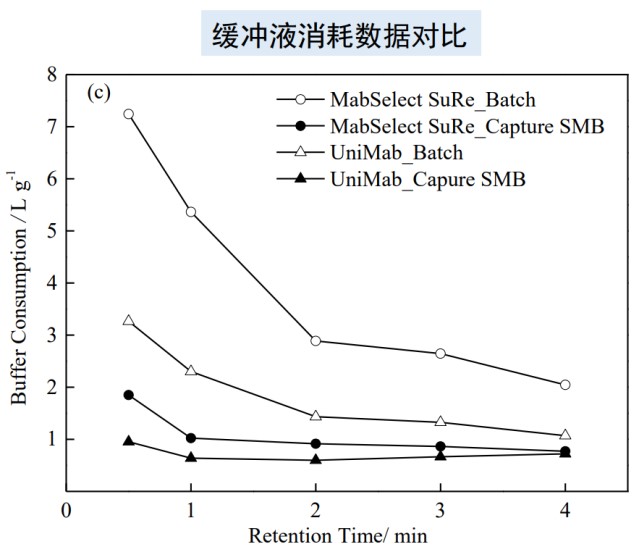
Comparison data of elution buffer consumption data of monodisperse and polydisperse affinity chromatography media
Continuous chromatography with 10 production batches of monodisperse UniMab medium purification monoclonal antibody with excellent chromatographic reproducibility
Repeatability comparison of chromatograms of 10 batches of monodisperse UniMab media purification
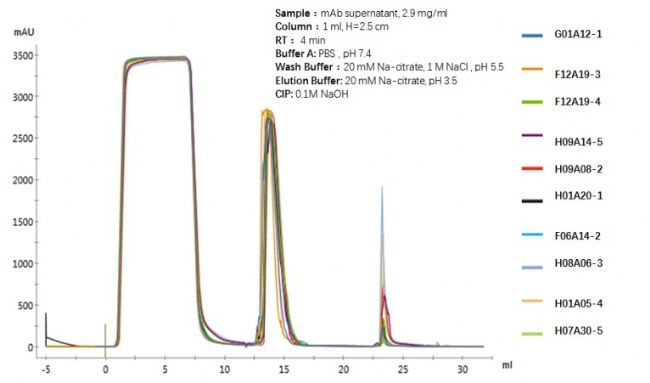
Data statistics of 10 batches of monodisperse UniMab media purification monoclonal antibody (up to 100L per batch)
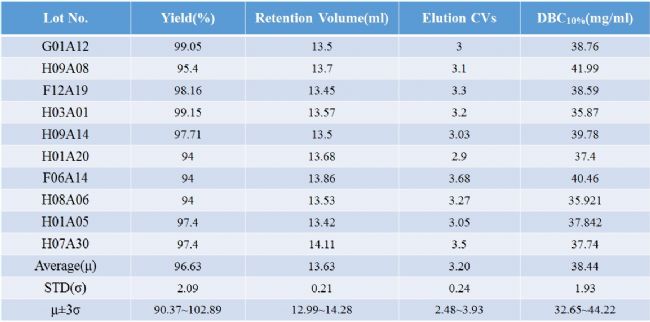
As shown in the above table, by repeating the investigation of the separation and purification of monoclonal antibody by ten production batch affinity media, it can be clearly seen that the monodisperse UniMab affinity medium maintains the ideal chromatogram in the separation and purification of the monoclonal antibody. The reproducibility and the stability of the affinity medium are ideal, which will bring convenience to the optimization and amplification of the production process of the enterprise and the research institute. In a certain sense, it is possible to ensure that production research is carried out efficiently to the greatest extent, and the consumption of production resources such as human and material resources is minimized.
Overview of Purification Data for Monolithic Applications Using Monodisperse UniMab and Polydisperse Soft Media
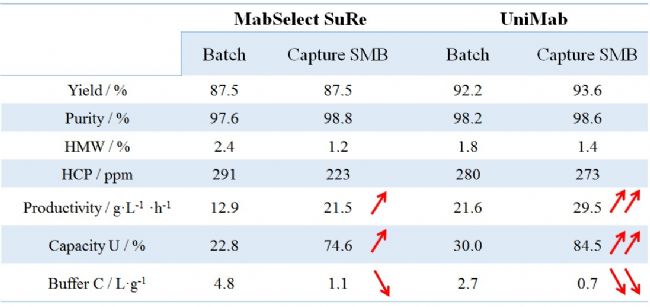
Purification data statistics of monodisperse UniMab and polydisperse soft media
In summary, we found in the experiment that continuous double-column loading can achieve efficient protein capture, significantly improve media utilization, improve space-time yield, reduce buffer consumption, and is especially suitable for Protein A affinity capture monoclonal antibody. As shown in the above table, the chromatographic performance of monodisperse UniMab and polydisperse soft media is basically the same in terms of purification data, recovery rate and HCP. However, in monoclonal antibody production efficiency, chromatographic media utilization and buffering. In terms of liquid saving rate, monodisperse UniMab has shown more significant advantages. These obvious advantages will greatly improve the production efficiency and economic benefits of pharmaceutical companies, save the cost of production materials and environmental protection costs, and ensure the cost. Users can carry out the separation and purification production or research of monoclonal antibodies more efficiently and quickly.
At the end of the article, Xiao Bian is willing to give readers a brief summary of some of the significant advantages of Nano-Protein A affinity chromatography media. It can be said that it is because of the purpose of innovation research that Nawei Technology has brought you a performance. This superior Protein A affinity chromatography medium. If you are interested in our products, please contact us by hotline to provide you with more detailed product information or sample equipment.
High mechanical strength, high dynamic load at high flow rates, can greatly improve production efficiency
Good alkali resistance, can meet CIP & SIP requirements
Long service life and low production costs
Significantly reduced buffer usage, further reducing production costs
High recovery rate, high purity of target antibody, low separation of HCP and loss of Protein A ligand
The world's first mass-produced monodisperse Protein A affinity chromatography media, ideal for continuous chromatography media
Nano offers a complete solution for cost-effective antibody purification
(Welcome to contact us directly for details)
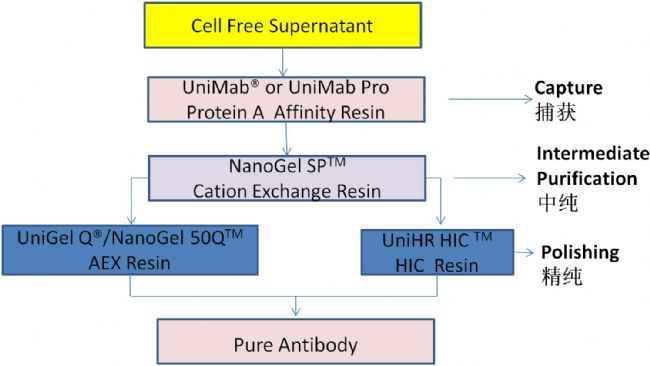
Remarks: Some experimental data in this article were provided by Professor Lin Dongqiang from Zhejiang University.
Video Door Phone,Intercom System For Multi Apartment,Ip Video Door Phone System,Video Door Phone Made In China,Video Intercom
Zhuhai Mingke Electronics Technology Co., Ltd , https://www.zhmkdz-electronics.com